Why Is Good Manufacturing Practices (GMP) Certification Important?
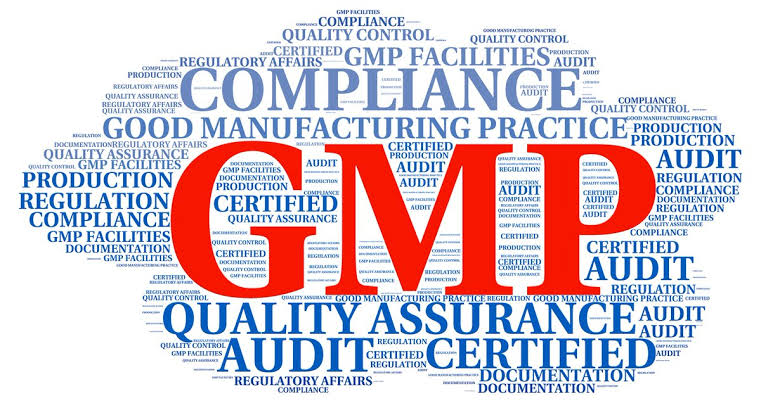
Organizations must optimize their manufacturing processes to release consistent, reliable, and quality backed products. Good Manufacturing Practices (GMP) are critical systems that seek to streamline and effectively control the design, monitoring, and evaluation of manufacturing processes and facilities. GMP exists to protect manufacturers and customers alike from any risks of faulty or malfunctioning products. GMP guidelines aid manufacturers in improving the production of goods. It is a part of quality assurance to mandate the production steps.
GMP regulations guarantee
- Uniformity
- Safety
- Effectiveness,
- It helps minimize or even eliminate mistakes,
- Prevent failures,
- Reduce health risks for manufacturers and consumers.
GMP effectively oversees every aspect of the manufacturing process, thus guarding against potential risks that can prove detrimental to products and the end-users. These practices are proactively revised and updated to meet the needs of the current age. It is highly flexible, enabling companies to adjust them to fit their specific needs while remaining compliant with the specific guidelines.
A good manufacturing practices certificate verifies and validates an organization’s basic manufacturing practices. It confirms that the company has effectively regulated the procedure to help the products meet the quality standards. GMP certification thus better protects manufacturers, consumers, and the environment from harm and helps reduce facility losses and waste. Organizations that leverage GMP certification can establish their credibility and authority and maintain customers’ trust. The end customers get the satisfaction that they are purchasing products manufactured in a safe, well-regulated environment that is compliant.
Five Main Components of Good Manufacturing Practice
Regulating GMP in the workplace is of paramount importance to the manufacturing industry. GMP focuses on the 5 P’s that enables compliance with strict standards across the manufacturing pipeline. The 5 P’s include:
- People: The workforce in an organization must strictly align to manufacturing processes and regulations. Business leaders must administer GMP training to understand their roles and responsibilities. Moreover, they should keep track of employees’ performance to identify the gaps and take necessary action to boost their productivity, efficiency, and competency.
- Products: Manufacturers must not compromise product quality in any manner. Before distributing, the products must undergo constant testing, comparison, and quality assurance. Every production stage must be monitored, and manufacturers must observe standard methods when packing, testing, and allocating sample products.
- Processes: Effective documentation of processes is crucial. The documents must be clear, consistent, and accessible to all employees. Organizations must regularly evaluate the working processes to establish that employees consistently comply with current processes.
- Procedures: It refers to a set of guidelines that allows the stakeholders to undertake a critical process or part of a process and achieve results with better consistency and accuracy. Organizations must ensure that the employees do not deviate from the standard procedure.
- Premises: It must ensure comprehensive cleanliness. Monitoring the premises will help prevent cross-contamination, accidents, or fatalities. Storing equipment, calibrating it, and ensuring its fit to produce consistent results helps prevent equipment failure
GMP standards apply to the production of:
- Food
- Beverages
- Cosmetics
- Pharmaceutical goods
- Dietary supplements
- Medical devices
Through GMP certification, companies can leverage the best systems to produce safe and effective products. GMP certification helps achieve the following:
- Prevent Damage to Health: GMP certification helps manufacturers avoid producing poor-quality pharmaceutical goods. If they do not properly control it, they may end up unintentionally adding toxic substances to products. It may end up having negative impacts on health.
- Defined and Controlled Hygiene Protocols: Consumable items have an immediate impact on the consumer’s body. Processes that incorporate GMP ensure that employees have adequate knowledge and training on hygiene protocols. GMP also applies to storage, testing, packaging, distribution, and recall.
- Cut Profit Loss: Poor quality products are a waste of money for the various entities involved, including manufacturers, customers, and the government. Manufacturers input time, money, and resources into the production process. Implementing GMP helps them regulate these processes to identify areas that trigger and tightly control practices to prevent loss of money and resources.
- Lessen Complaints and Avoid Recalls: Industries need to win the trust of customers. Companies face cut-throat competition in the marketplace, and if they fail to deliver as per customers’ expectations, their business will suffer drastically. Poorly produced goods may have a negative impact on your company. It can affect your credibility and business potential. It triggers recall, and customer complaints tend to add unnecessary manpower. You need to assign a team to look after recalls and refunds. Instead, incorporating GMP helps lower the incidence of recall, thus reducing the workload. Moreover, it will result in customers providing good and favorable reviews, improving your business image.
- Boost Export Opportunities: Incorporating GMP certification provides international recognition to your business. Thus, more customers, suppliers, and vendors will seek to associate with your company. It will thus enable you to expand your market share and improve your business potential.
To Conclude:
GMP certification ensures that manufacturers produce goods consistently and in a controlled manner. It is of valuable importance to organizations to maintain high-quality standards for their products.